Lack of access to relevant and up-to-date documentation for work equipment can lead to several problems in the workplace. It can also result in non-compliance with the EU Machine Directive, which lays out the requirements for machinery and equipment including access to information.
Has your company experienced any of the following challenges because employees did not have access to documentation about the equipment they use when they needed it?
- Interruption of operations or lower productivity, because of time spent finding certificates, operating instructions and/or inspection reports.
- Breach of central regulations, because employees lacked access to documentation about the condition and correct use of the equipment.
- Increased costs for maintenance and repair, because the equipment isn't used according to the user manual.
- Accidents, because the equipment was used incorrectly or wasn't approved.
- Loss of customer relations, because goods have been damaged or for the reasons mentioned above.
The list is by no means exhaustive. There are many issues arising from poor equipment management that can impact businesses on all levels - from the effectiveness of their daily operations, to their reputations and bottom-line.
The solution: a digital tool
Digital tools open up a whole new level of safety and efficiency when used to manage equipment documentation and compliance. To succeed with digital tools there should be a focus on the following aspects:
- Digital storage: For employees to access digital tools from mobile workplaces, it's essential that equipment documentation is stored and accessed from the cloud. This enables documentation to viewed and reports to made from anywhere, while being uploaded and shared with all stakeholders.
- Suppliers and inspectors doing the equipment input: Enable suppliers and inspectors of work equipment to upload documentation and reports for new or inspected equipment directly into digital tools. With access for all stakeholders, equipment owners can save valuable time.
- Mobile apps: Apps give employees access to documentation straight from their smartphones or tablets. These can also be used to document use and enter important data about the equipment.
- Training: The apps facilitate training in the workplace. Feel free to let the suppliers show you how to use the equipment.
- Tracking: Use QR codes or tags on work equipment. These can be used to track the equipment's location, availability, status, history and documentation.
- Notifications: Notify employees via the app when important documentation is updated or even when equipment must be returned.
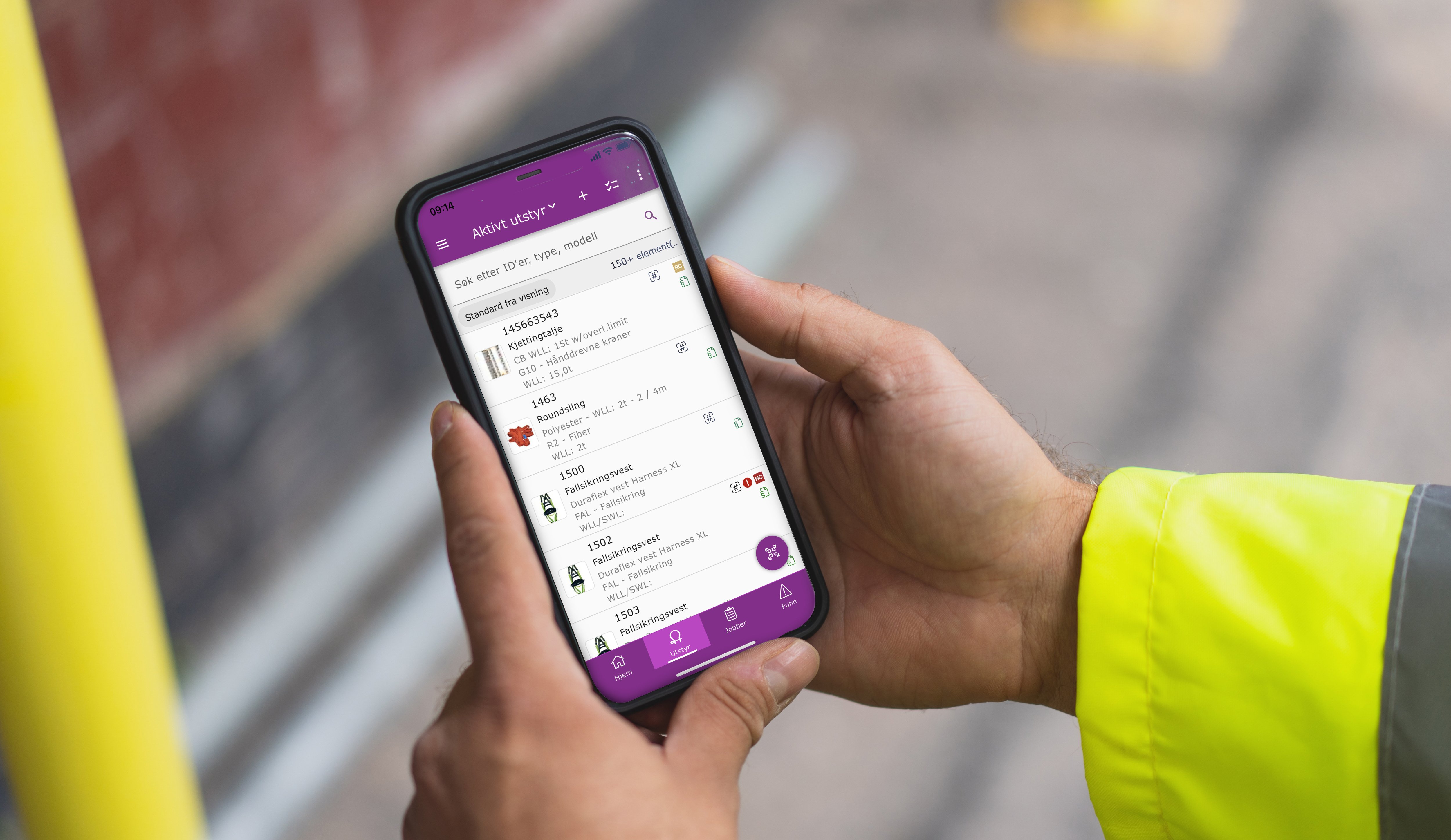
A worker using the Onix Worker app to access documentation for work equipment.
Benefits of easy document access for employees
Access to up-to-date and relevant documentation can create a wide range of positive effects, particularly within health, environment, and safety. Among these are:
- Improved safety: Up-to-date documentation provides essential information about the equipment's safety functions, operating procedures, weight limits, previous checks, and more. This can encourage better use, reduce the risk of equipment failures and prevent accidents
- Better productivity: Detailed manuals and instructions guide employees on the correct use of work equipment. Correct set-up, operation, and dismantling help ensure that the equipment is used correctly and most efficiently.
- Faster and cheaper checks: When inspectors of the equipment has easy access to documentation, they can increase inspection efficiency by up to four times. That saves you time and money.
- Better training: When employees have access to the correct documentation about work equipment, it facilitates more comprehensive and accurate training. This encourages correct, safe and more efficient use.
Use Onix to digitalize equipment management
Onix Work offers a complete solution to digitalize equipment management and help realize the above benefits.
Onix Work is an open equipment compliance management system (ECMS) that allows all stakeholders (equipment owners/users, inspector and suppliers) to access crucial documentation and collaborate in one place.
Equipment users can access documentation and report deviations on-site by scanning QR, RFID or NFC tags. Equipment owners can track and manage equipment use and schedule maintenance. Inspectors can identify and update equipment documentation, and suppliers can provide original documentation when equipment is delivered. This takes place all in one digital, accessible place.
The result? Improved safety, compliance and efficiency.
Are you ready to try Onix?